
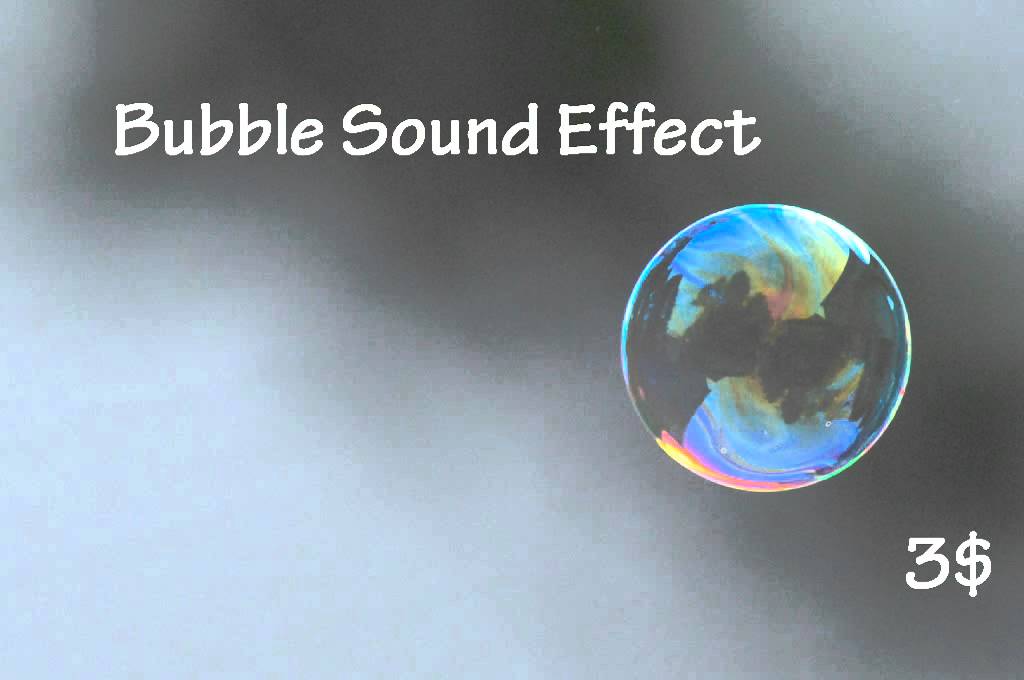
Check firing temperatures using pyrometric cones.ģ. Slower firing cycle or longer soaking period.Ģ.
#BUBBLE CRACKLE GLAZE EFFECT FREE#
Precipitation taking place during cooling of the glaze.Ī) The appearance of small crystals on the surface of the glaze such as calcium or zinc silicates.ī) Milky precipitate such as calcium borate.ġa) Cool more quickly down to 700☌, that is, whilst the glaze is still semi-molten.ġb) Reduce the lime content of the glaze.ġd) Use low solubility glaze instead of lead free glaze.ġ. The body should have a higher expansion rate than the glaze to maintain the glaze under compression.Ī) Fire the body to a higher temperature.ī) Soak the body for longer time at the peak temperature.Ĭ) Increase the silica content of the body.Į) Add silica or china clay to the glaze.į) Use borax frit of lower expansion rate. Add Barium Carbonate (1-2.5%) to the clay body to precipitate the soluble salts.įine cracks showing in the surface of the glaze.Įxpansions. Handle dipped ware very carefully reduce the clay content of the glaze.Ĥ. Minimize the handling of the bisqueware before glaze application.ģ. Excessive colloidal matter (clay) present in the glaze.ġ. Cracking of the glaze layer during drying and before firing. Oil, grease, dust on ware before glazing.ģ. Excessive handling of dry clay ware be fore glazing.Ģ. Slow down the initial firing rate to 2-4 hours.īare (unglazed) patches on the surface of pottery.ġ. Invert mugs, jugs, bowls when they have sufficient strength.Ĥ. Over working of the clay during forming.ġ.

Presence of impurities in the clay or glaze.Ī) Particles of plaster from the surface of the mould.ī) Sulphates and/or carbonate present in the body.ġb) Remove any plaster plucked away from the surface of the mould.ĥ. Expansion of the body produced by pressure build up of gases trapped in a partially vitrified body.ī) Carbon trapped within a vitreous body.ġc) Reduce the flux content of the body and/or add grog to produce a more open body.ġ. Use coloured stains instead of metallic carbonates, especially manganese dioxide.īubble formation within body during firing.ġ. Lower firing temperature or alter body fluxesģ. move pottery away from edges of kiln shelves.Ģ. use nepheline syenite to replace some feldspar in stoneware glazes.ġd) Use wollastonite instead of whiting or dolomite in stoneware glazes.ġe) Often only near elements or flame flashing in gas kilns i.e. Low thermal mass – fibre kilns – can cool too rapidly.ġa) Slow down temperature rise to top temperature over the last 50☌.ġc) Alter glaze to a more fluid state e.g. Very rapid firing at maturity, does not allow glaze to mature.Ĥ. In gas kilns, flame impingement will cause the fault.ģ. Innumerable craters, bubbles and pinholes in the surface of the glaze.Ī vitrified body with minute bubbles on the clay surface, that are sometimes only evident by roughened surface.Ģ. Listed below are some of the most common faults and their remedies, which we have collated over the years. Walker Ceramics is proud of the technical support and after sales service we provide.
